Surface mounting is attaching a fence or screen to a solid surface. The surface could be a wood deck, concrete patio, sidewalk, or driveway.
Any WamBam vinyl fence or aluminum fence can be mounted to a wood, or concrete surface using our vinyl surface mounts or aluminum surface mount post.
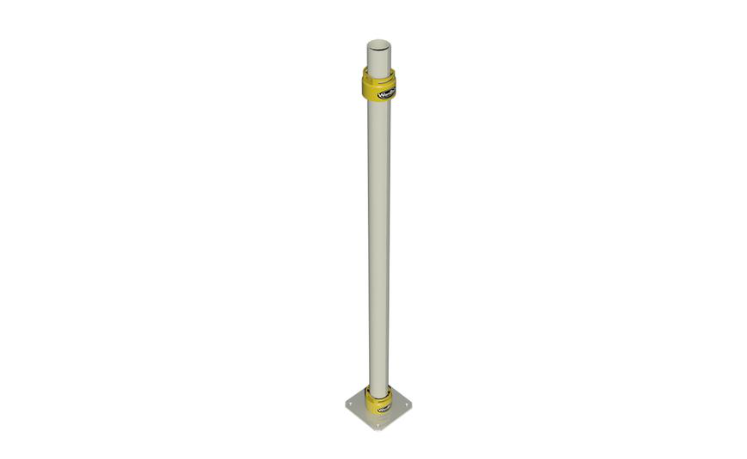

Please see below for installation instructions on various surfaces. Installation of our vinyl surface mount onto concrete can be viewed here, but the concept is the same for aluminum surface mount posts or Zippity surface mounts for shower kits:
Surface Mounting to Concrete (shown in video above)
Before mounting on your concrete surface, make sure that the concrete is 4” thick or more. It is best to mount 2” or more away from the edge of the concrete to prevent cracking.
- Place the surface mount at the intended location and mark where the holes are.
- Set aside the surface mount.
- Using a hammer drill, make holes 2″ deep in concrete where they are marked from the surface mount.
- Place surface mount back at the intended location.
- The newly drilled holes should match up with the holes in the base of the surface mount.
- Secure to concrete with wedge anchors.
- Use 3/8″ x 3” long wedge anchors if you are mounting a vinyl post.
- Use 1/4″ x 2.25″ long wedge anchors if you are mounting an aluminum surface mount post.
- Do not use concrete screws or blue screws.

Surface Mounting to Wood or Composite Decking
If you have access under your wood deck, please mount an additional 2×6 or 2×8 wood block underneath your deck surface. This is to alleviate stress from bolts attaching surface mount to the wood floor. If your deck surface is composite, please know this step of adding a wood block is even more critical as composite decking is not as hard as wood decking. Afterwards, continue with steps below.
- Place the surface mount at the intended location and mark where the holes are.
- Set aside the surface mount.
- Drill holes through both the deck surface and the additional wood blocking.
- The newly drilled holes should match up with the holes in the base of the surface mount.
- Using 3/8″ x 4” diameter bolts, washers, and nuts; secure from the underside of deck. Do not use wood screws or lag bolts.
Mounting to Thin Concrete
If concrete is less than 4in. thick, you may want to attempt drilling directly through it so you can insert one of our pipe anchors through it and into the ground, as illustrated below.
A. Mark holes for drilling.
B. Use a 1-5/8″ concrete drill bit (for vinyl pipe anchors) or 1″ concrete drill bill (for aluminum pipe anchors), extension if needed, and a concrete hammer drill.
C. Drill both pre-marked holes completely through concrete.
D. Pound pipe anchors through holes in concrete to recommended depth.
E. Trim prongs from anchor positioner along bottom edge.
F. Install post over pipe anchor. If necessary, see fence instructions for more information on how to install anchors, adjust leveling donuts and install posts. A vinyl post is pictured above.
Another (Least Preferable!) Option: Chain Drilling to Create a Hole in Concrete
If you only have a few holes to create, and don’t have a drill bit large enough to accommodate your pipe anchor diameter, you may want to consider using a drill to create a 1-5/8″ or 1″ hole.
Please note: Mounting on pavers or brick is not recommended
Generally, most pavers and brick are not cemented in. They sit on top of granular sand/gravel or sometimes over concrete. Do not use our surface mounts in these cases. You can drill through your paver or brick (although it may crack!) and pound pipe anchor into the ground below it. Another option is to remove paver, install post in ground, then cover ground around installed post to your liking.
What about asphalt?
You cannot use surface mounts on asphalt. It is not hard enough. You can drill through the asphalt or use a blow torch to soften it and then drive the pipe anchor through the hot, soft asphalt into the ground beneath. Install post over pipe anchor as per instructions.